Fasteners and Machining: Important Parts for Precision Manufacturing
Fasteners and Machining: Important Parts for Precision Manufacturing
Blog Article
Browsing the Globe of Fasteners and Machining: Approaches for Accuracy and Rate
In the intricate realm of fasteners and machining, the mission for precision and speed is a continuous challenge that requires meticulous focus to detail and strategic planning. From recognizing the varied range of fastener types to selecting optimal materials that can endure rigorous needs, each step in the process plays a crucial duty in achieving the wanted end result.
Understanding Fastener Kind
When selecting bolts for a task, understanding the numerous types offered is critical for ensuring ideal performance and integrity. Bolts are utilized with nuts to hold products with each other, while screws are functional bolts that can be utilized with or without a nut, depending on the application. Washing machines are essential for dispersing the lots of the fastener and stopping damage to the material being attached.
Selecting the Right Products
Recognizing the relevance of choosing the right materials is extremely important in ensuring the ideal efficiency and integrity of the chosen fastener kinds discussed formerly. When it concerns fasteners and machining applications, the material option plays a vital role in determining the general toughness, longevity, deterioration resistance, and compatibility with the intended setting. Various products supply varying buildings that can dramatically affect the performance of the bolts.
Usual materials used for fasteners consist of steel, stainless-steel, aluminum, titanium, and brass, each having its special staminas and weaknesses. Steel is renowned for its high strength and durability, making it suitable for a wide variety of applications. Stainless steel provides outstanding deterioration resistance, perfect for settings vulnerable to moisture and chemicals. Aluminum is corrosion-resistant and light-weight, making it ideal for applications where weight decrease is vital. Brass is commonly picked for its visual allure and exceptional conductivity. Titanium is understood for its outstanding strength-to-weight ratio, making it perfect for high-performance applications. Choosing the ideal product includes thinking about aspects such as strength demands, ecological conditions, and budget restraints to guarantee the desired performance and longevity of the fasteners.
Precision Machining Techniques
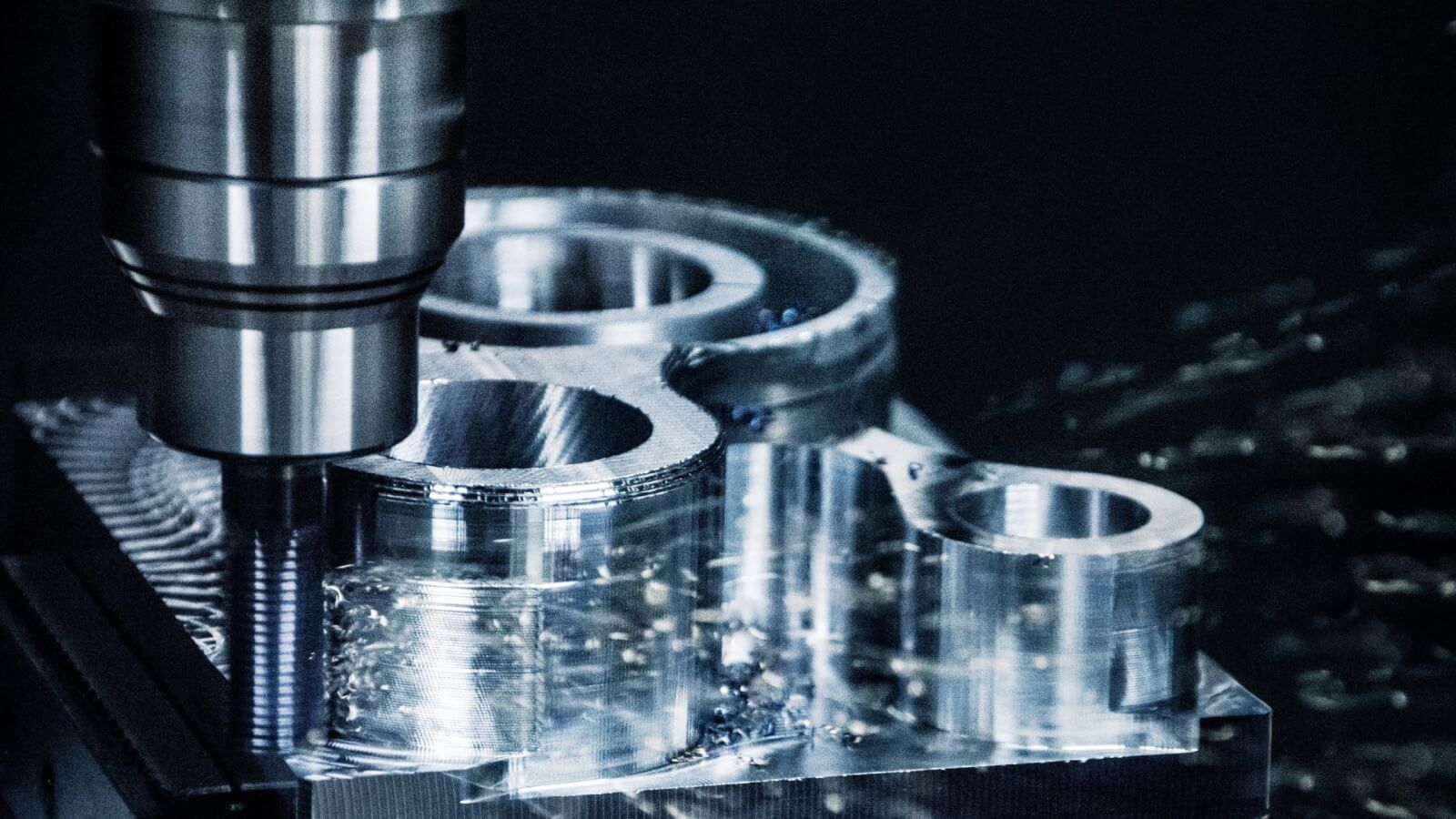
Along with CNC machining, various other accuracy strategies like grinding, transforming, milling, and exploration play essential functions in fastener manufacturing. Grinding aids attain fine surface coatings and Learn More tight dimensional resistances, while transforming is usually used to produce round parts with precise diameters. Milling and exploration operations are important for shaping and creating openings in bolts, guaranteeing they satisfy exact specs and feature properly.
Enhancing Rate and Effectiveness
To enhance fastener production processes, it is essential to enhance procedures and carry out reliable methods that enhance accuracy machining strategies. Automated systems can deal with repeated jobs with precision and rate, allowing workers to focus on even more complicated and value-added tasks. By combining these techniques, makers can achieve an equilibrium between speed and accuracy, ultimately improving their affordable side in the fastener market.
High Quality Control Steps
Carrying out extensive quality control steps is critical in ensuring the reliability and uniformity of bolt items in the production procedure. Fasteners and Machining. Quality control procedures include numerous stages, starting from the option of raw products to the final inspection of the completed bolts. This includes evaluating elements such as material make-up, sturdiness, and toughness to ensure that the bolts satisfy market requirements.
Normal calibration of devices and equipment is crucial see here to keep uniformity in manufacturing and make certain that fasteners satisfy the necessary resistances. Applying stringent protocols for identifying and attending to problems or non-conformities is important in stopping substandard products from entering the marketplace. By developing a detailed quality assurance framework, suppliers can promote the track record of their brand and deliver fasteners that satisfy the highest possible criteria of performance and this hyperlink toughness.
Verdict
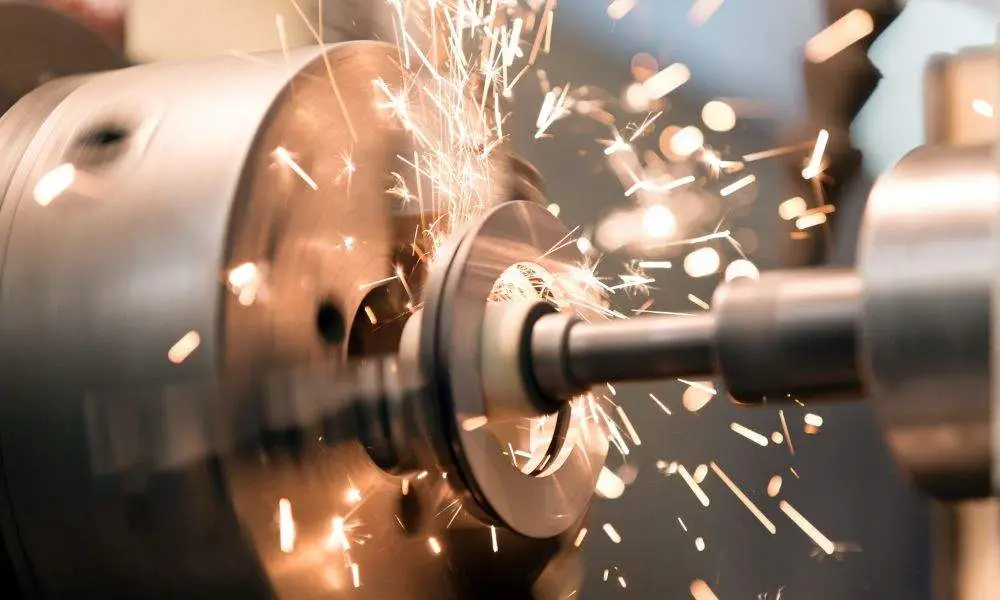
In the intricate world of bolts and machining, the quest for accuracy and rate is a continuous difficulty that requires meticulous focus to detail and tactical preparation. When it comes to fasteners and machining applications, the material choice plays an essential duty in determining the overall toughness, longevity, deterioration resistance, and compatibility with the desired environment. Precision machining includes numerous innovative techniques that ensure the tight tolerances and specifications needed for bolts.In addition to CNC machining, other accuracy methods like grinding, turning, milling, and drilling play vital functions in bolt production.To optimize fastener production procedures, it is necessary to streamline operations and implement efficient approaches that complement precision machining techniques.
Report this page